Our journey so far
Transition from fossil fuels to green energy
From 2016 - 2021 we transitioned our energy consumption so that we do not use fossil fuels in our production and for heating.
Our transition is based on 3 pillars:
Reduction of
energy consumption
Electrification of
energy consumption
Use of
green energy
Since 2016 we have invested in several more energy efficient solutions:
- 8 solar power plants with a total annual production of approx. 1,200,000 kWh
- Installation of batteries with a capacity of 943 kWh
- Replacing all gas-fired boilers for heating with heat pumps
- Replacing an oil-fired boiler for our paint shop with heat pumps
- Installation of heat exchangers that recapture approx. 75% of the heat from the exhaust air of the paint shop and the welding processes.
- Replacing fossil fuel cars with electric ones
- Installation of charging stations for charging electric cars
- Change to electric forklift trucks
- Reducing our energy consumption e.g. by installing LED lighting and energy-optimised production machinery
- Reducing our annual CO2 emissions by min. 300,000 kg on heating alone
- Reducing our total annual CO2 emissions by 440,000 kg
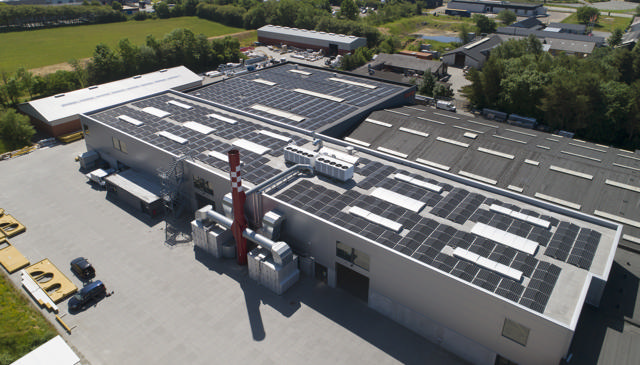
2016
We replaced all light sources with LED lighting and realised savings of 20% compared to earlier.
We purchased a fibre laser cutter which cost approx. 20% more compared to a traditional CO2 laser cutter, but only uses ⅓ of the energy during the cutting process.
We purchased a bending machine with a higher performance, but lower energy consumption due to a more intelligent control system.
We installed an air curtain with electric heating above the gates of our production halls. They channel warm air downwards when the door is open. This barrier of warm air insulates in winter and reduces draughts in the production area.
We replaced gas-fuelled forklift trucks with electric ones.
2017
We started converting from gas- to electricity-based heat production.
We installed two solar panel systems which annually generate 200,000 kWh.
2018
We replaced the ventilation system in one of the offices, so gas is no longer used for heating. A better ventilation control reduced the power consumption.
We installed 10 charging stations for charging electric cars.
We started selecting steel suppliers based on the CO2 emissions from the production of the steel and the subsequent transport to our facility. Some steel mills emit approx. 3 times more CO2 when producing the same type of steel. We have decided to buy from the manufacturers with the lowest carbon emissions.
2019
We replaced 4 fossil fuel cars with electric ones.
We built a new 2,500 m2 production hall. All energy-efficient solutions were considered from the beginning.
The paint shop and the entire building are now heated by heat pumps instead of gas and oil. The oil-fired boiler alone used around 11,000 litres of heating oil annually. 2 heat exchangers recapture around 75% of the heat from the painting process.
On the roof of the building, we installed our 3rd solar panel system with an annual capacity of 220,000 kWh.
Later that year we installed our 4th solar panel system with an annual capacity of 180 000 kWh.
2020
We installed our 5th solar panel system with an annual capacity of more than 400,000 kWh.
We installed 5 batteries with a total capacity of 400 kWh so that we can also use the solar cell power for operation at night and in the early morning hours when the sun is low in the sky. The system was prepared for a future expansion of 7 batteries.
We replaced the remaining gas-fired boilers for heating with heat pumps.
We replaced 4 more fossil fuel cars with electric ones.
We added insulation in our oldest production building.
2021
This year we received our first electric transporter.
We installed 7 additional batteries. Total capacity was now increased to 943 kWh.
We installed 2 more heat pumps.
We made an agreement with a steel supplier to have our steel transported with trucks running on HVO diesel. (Read more here: aGreenment (website in Danish))
We made an agreement with Air France/KLM to compensate our flights with bio-based SAF (Sustainable Aviation Fuel).
2022
We installed additional air curtains with electric heaters above more the gates.
2023
We installed our 6th solar panel system which increased our capacity by approx. 10%
We partnered with SSAB to purchase fossil-free steel from 2028.
We replaced our 2 final gas-fuelled forklift trucks with electric ones.
2024
We installed two additional smaller solar panel systems on our warehouses, increasing our overall capacity by 10%
2025
We produced our first low emission steel construction. This construction is a belt conveyor.
The production of low emission steel emits less than 500 kg CO2e per 1000 kg of steel produced. This is approx. 75% less than the emissions from the production of conventional steel produced using traditional methods. Here, emissions are around 2000 kg CO2e per 1000 kg of steel.